
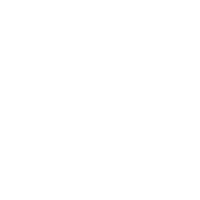

分析要点
轻量化设计是结构设计中永恒的话题,以汽车为例,不仅传统的燃油车要考虑燃油经济型,要考虑碳排放是否超标,新能源汽车出于对续航里程的考虑也必须将轻量化做到极致。若汽车整车重量降低10%,燃油效率可提高6%-8%,汽车整备质量每减少100公斤,每公里CO2排放量将减少8.5kg,同样在航空航天工业飞速发展和传统装备制造业同质化竞争加剧的今天,新产品总体性能的提升、生产成本的降低以及研发周期的缩短等成为设计人员不懈追求的目标。
传统轻量化设计大多是基于经典结构的等效替换,通过新工艺、新材料等精益改善和挖掘结构潜能,现已趋近“天花板”。
传统的结构轻量化多依赖工程师的经验设计,在设计改进后进仿真或实验验证进行重复修改迭代循环以趋近目标。优化设计结果要能够直接应用于工程生产实际还需要考虑产品应力、工程特征、制造工艺条件等,周期长,成本高且实现困难。
技术优势
对此我们引入拓扑优化技术和先进的优化工具,通过定义材料属性、载荷工况与约束条件,寻求给定设计域内材料的最优分布形式,在前期设计阶段大幅度缩短项目的开发周期,并在满足性能目标的前提下使得结构设计最优。
为满足工程实际的需要在结构拓扑优化设计中同时施加应力约束、工程特征约束和制造工艺约束等,如把槽孔、耳片、接头、凸台等这些满足装配需求和连接要求的工程特征考虑在拓扑优化设计中,以避免后续人为地添加这些特征。在保证优化结果基础上引入了最大/最小尺寸、拔模方向、模式重复、模式组、挤压约束等生产制造约束以适应实际生产。
现已应用于航空航天、汽车制造等领域。例如,应用填充微观点阵结构的卫星支架多尺度拓扑优化设计,使卫星支架减重 17% ,动态响应减少 25% ;考虑切口、保持传统钣金轮廓的涡轮发动机支架的拓扑优化设计,使发动机支架减重2 5 %,考虑增材制造工艺,扩大设计空间的拓扑优化设计,使发动机支架减重6 6 %,最大位移减少约5 0 %;由3 0 多个单独部件组成的稳定器前翼梁支架,应用拓扑优化一体化设计,成功实现前翼梁支架减重3 0 %,显著改善结构性能,提升加工效率。
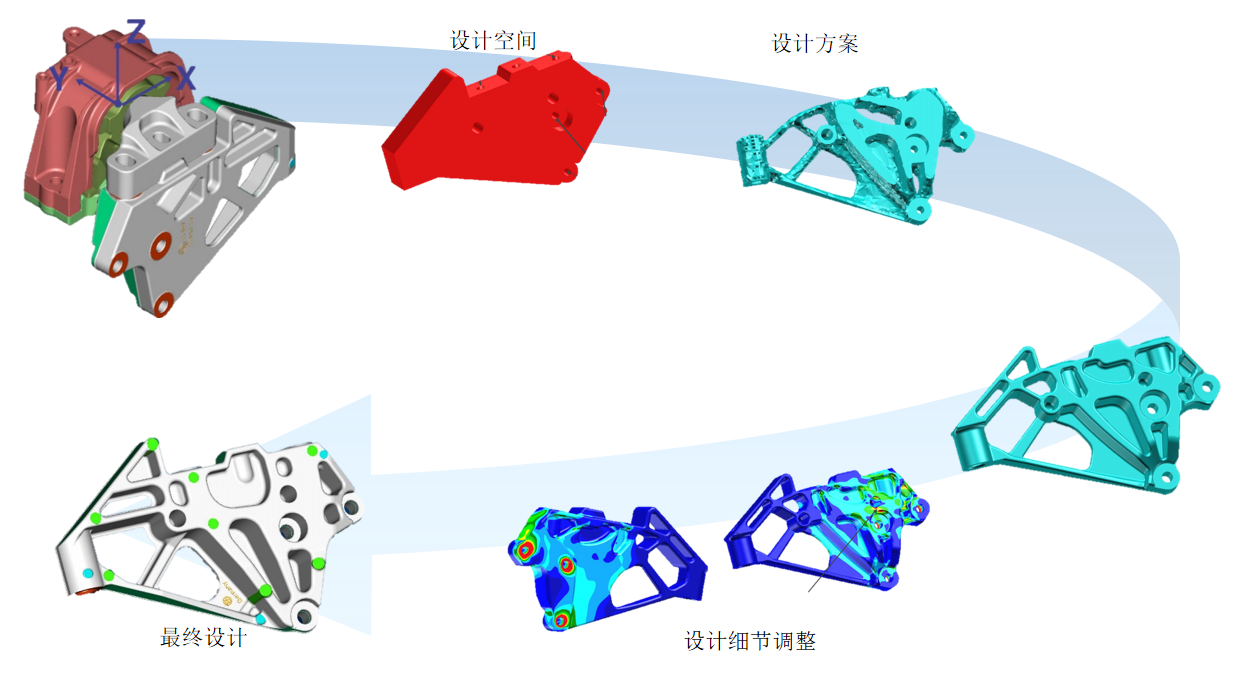
成功案例
精冲压力机机架减重优化
某公司生产的12000 kN精冲压力机机架。该机架采用不同厚度(30 mm~390 mm)的Q235-A钢板焊接而成,并采用整体退火处理。机架要承受全部的工作载荷,因此其机械性能直接影响整机的工作性能;另一方面,机架体积大、耗材多,通常重量占整机重量的60%左右,其结构轻量化对于整机的轻量化、减少生产和运输成本具有重要意义。因此,有必要对精冲压力机机架进行结构优化设计。
为保证精冲压力机的工作精度,一般情况下机架应满足以下性能要求:
1)具有较好的结构强度,最大工作应力应在许用应力范围内;
2)具有较好的整体刚度,整体刚度可以用额定载荷下的结构应变能或柔度(Compliance)来衡量;
3)具有足够的局部刚度,即受力面和导向面(如图1c所示,由于对称性,只标出两个导向面位置)的变形要在指定范围之内;
4)具有良好的动态特性,要求机架的固有频率远离激振频率,以避免共振。
优化流程详情:
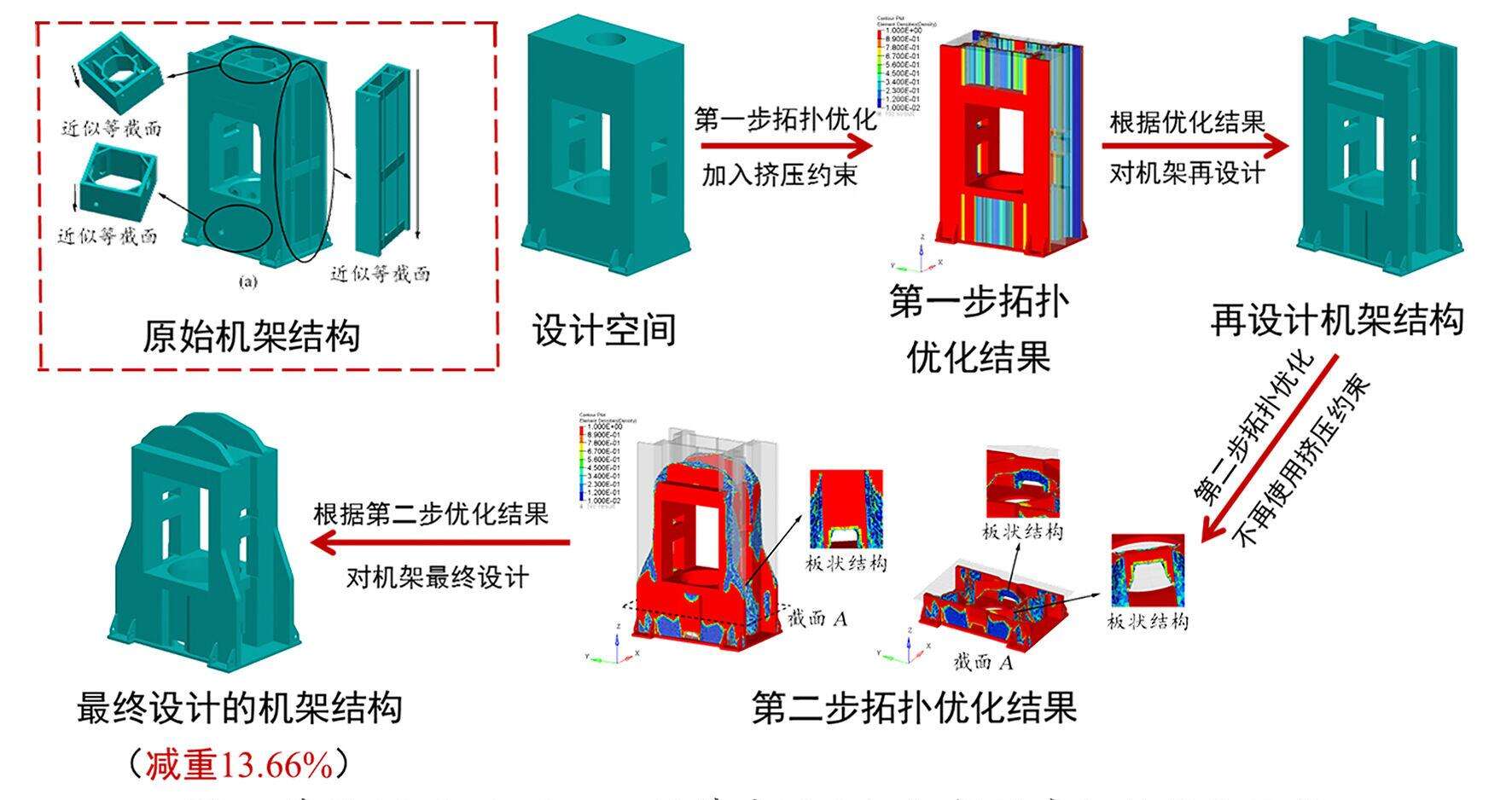
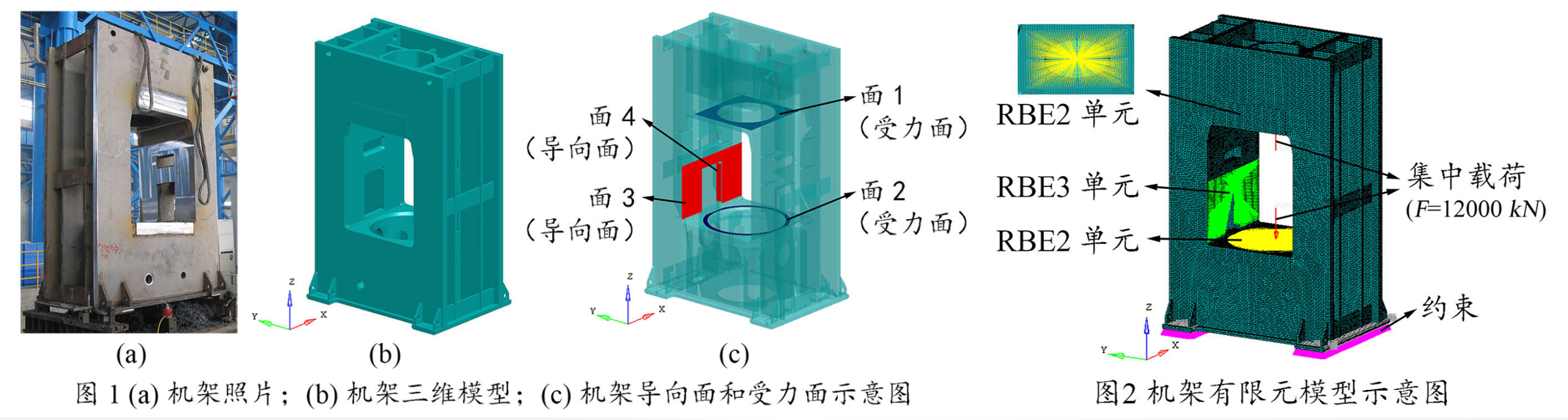
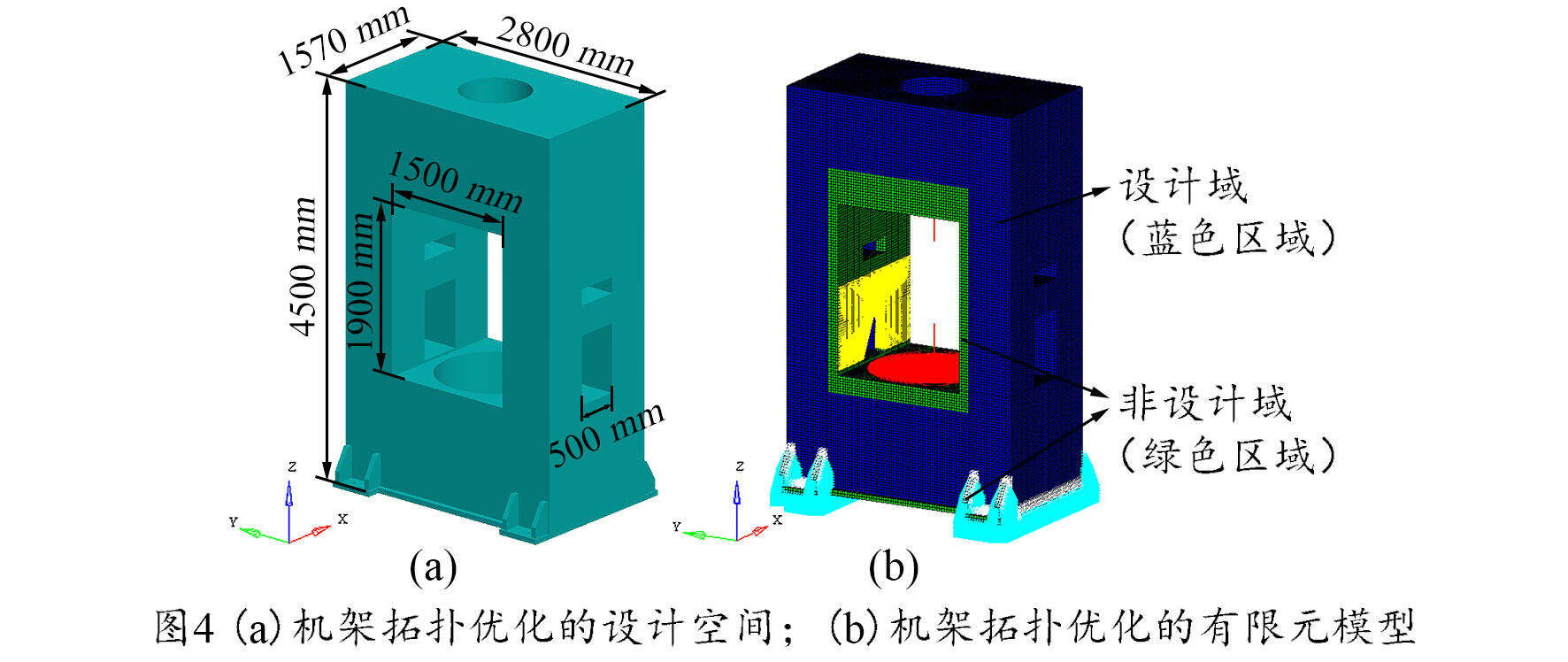
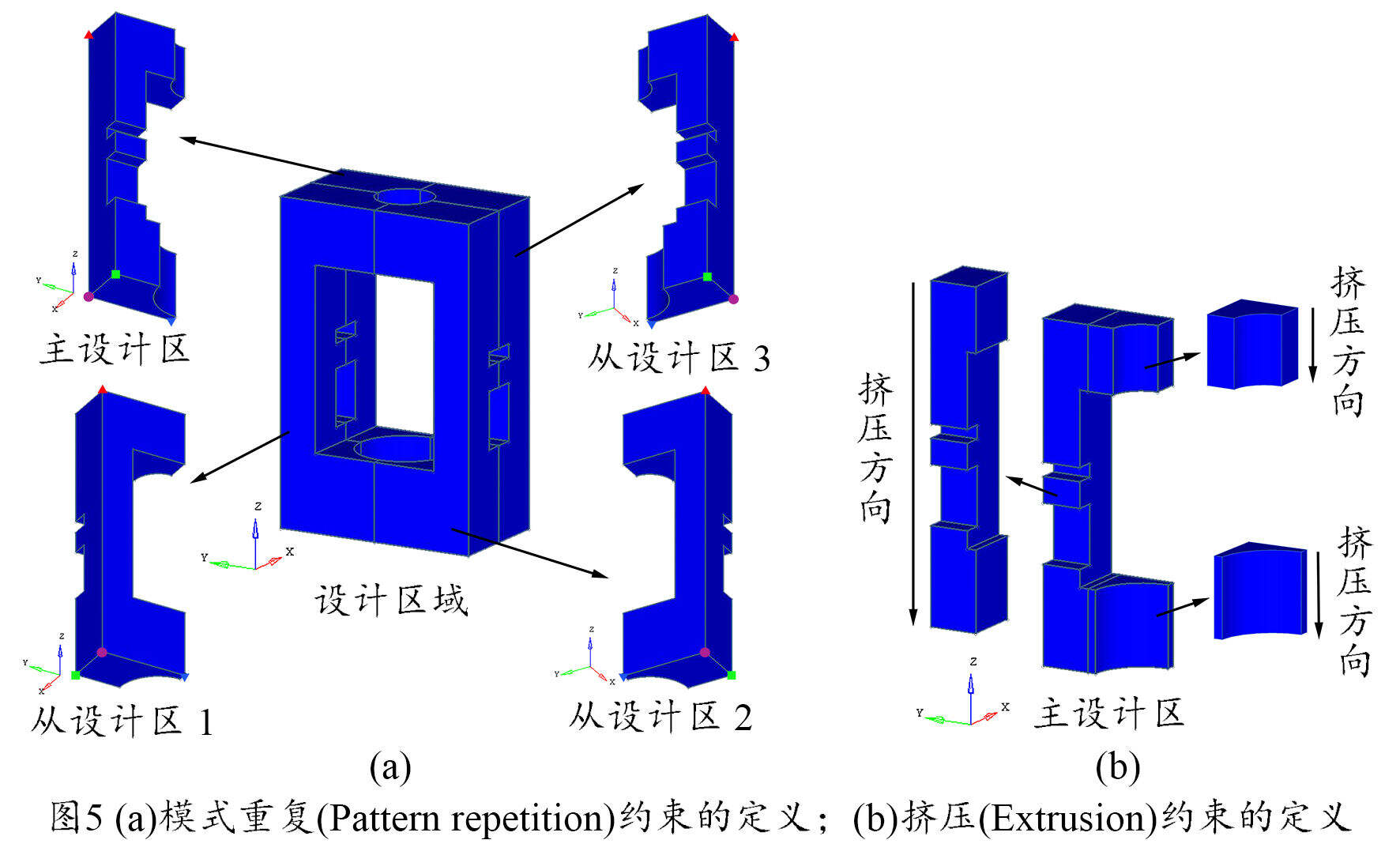
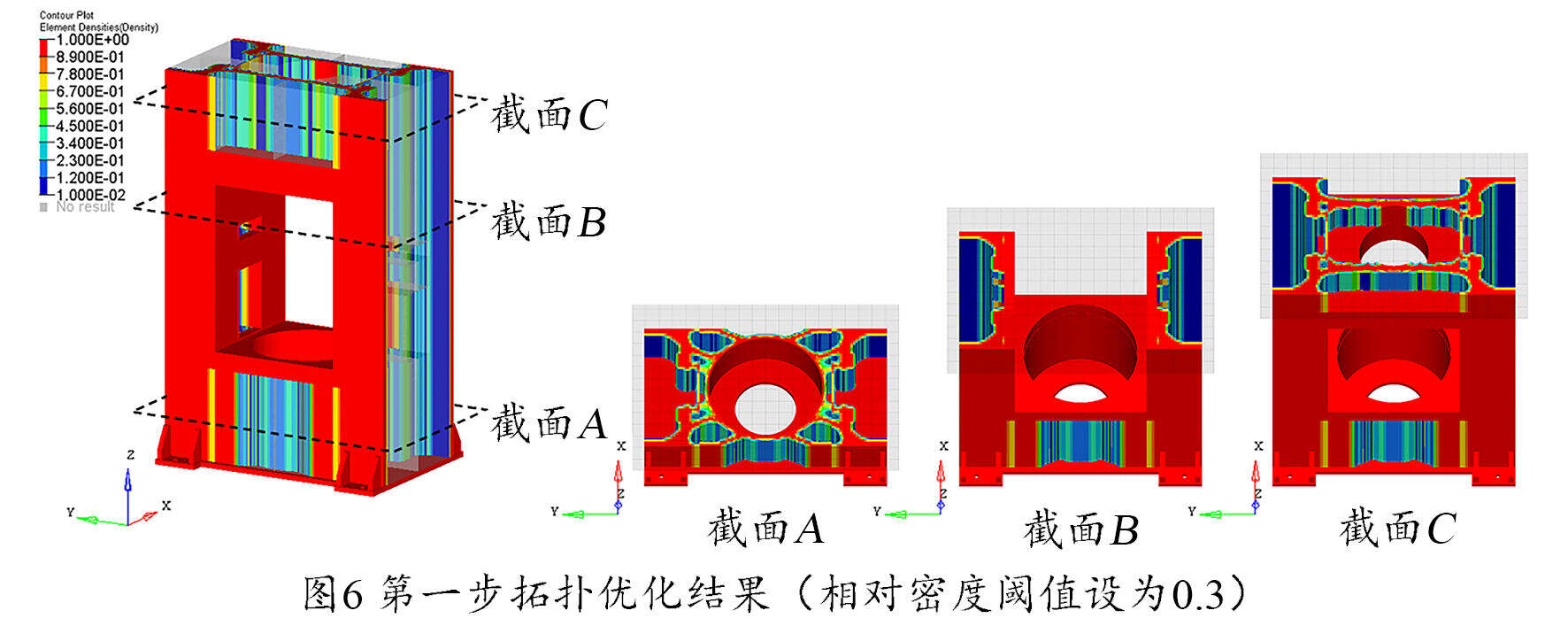
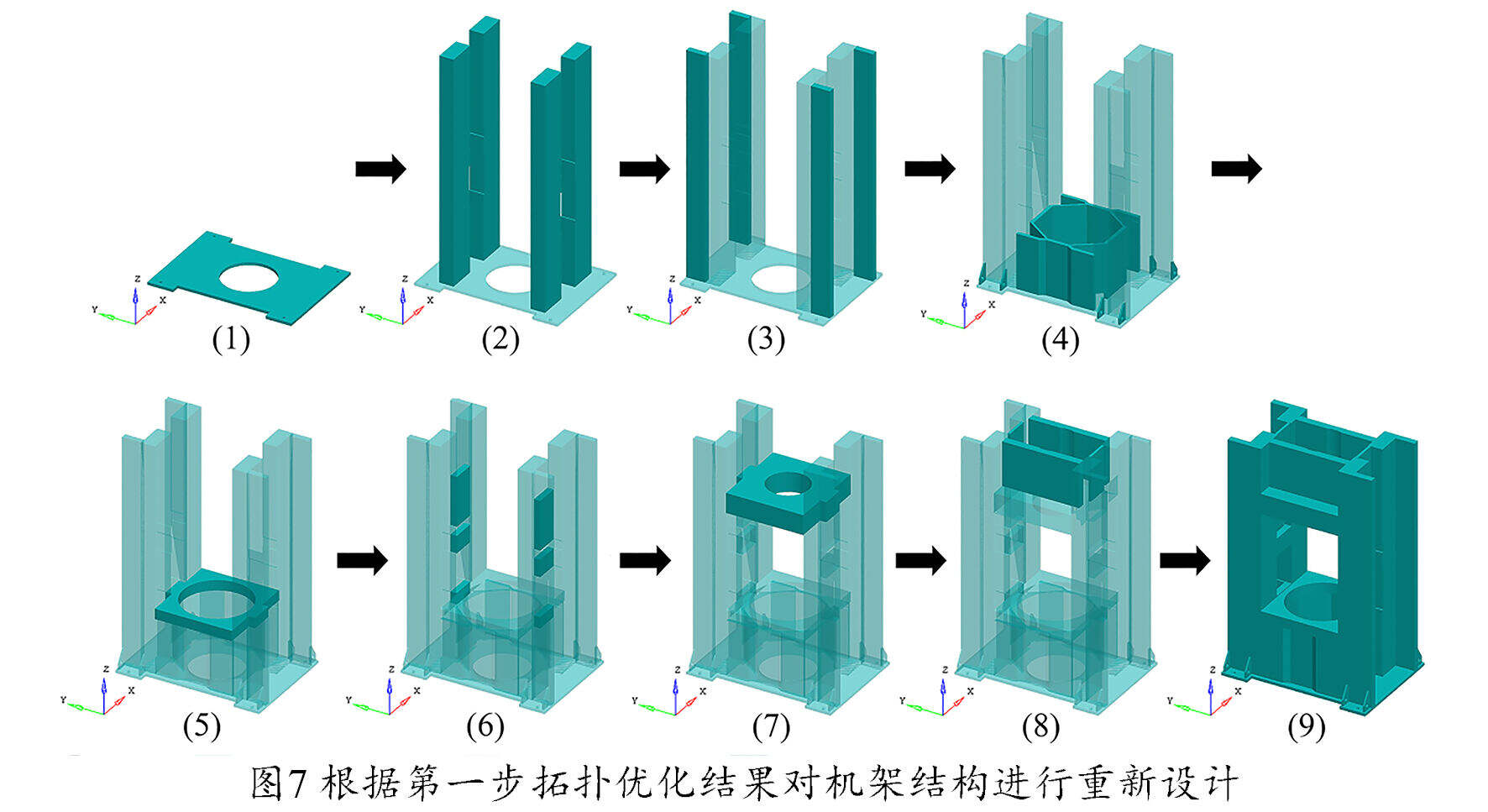
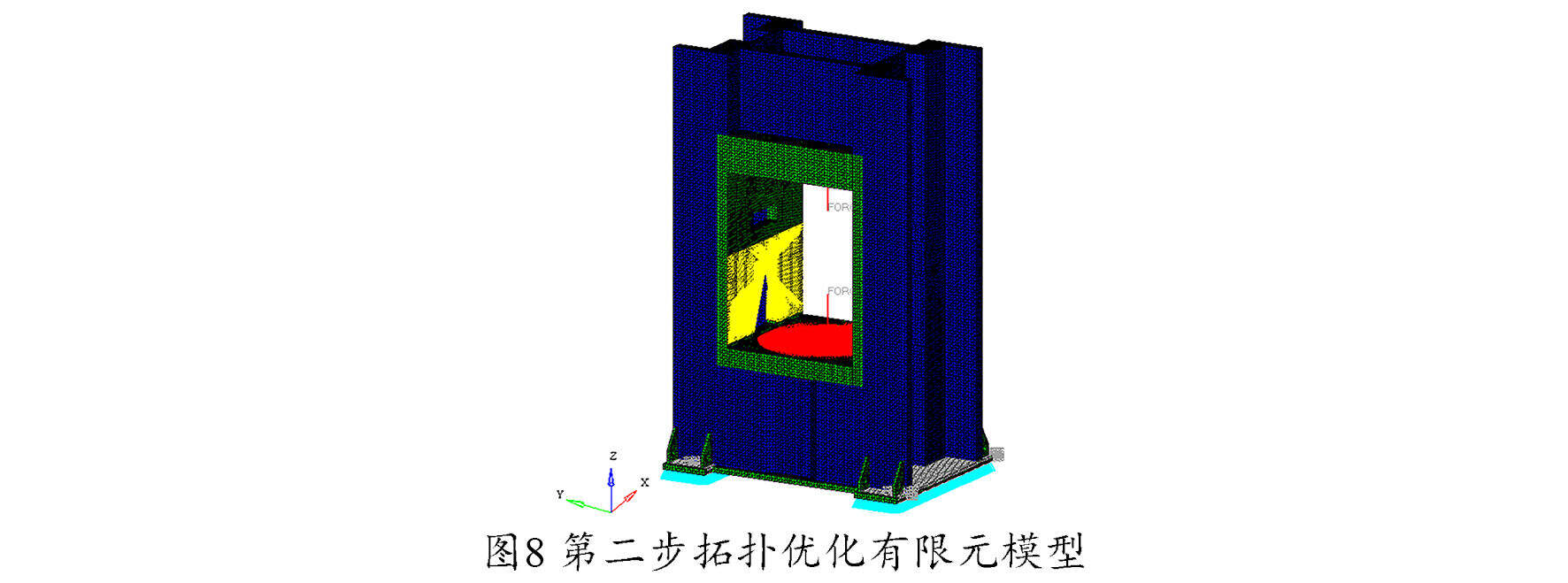
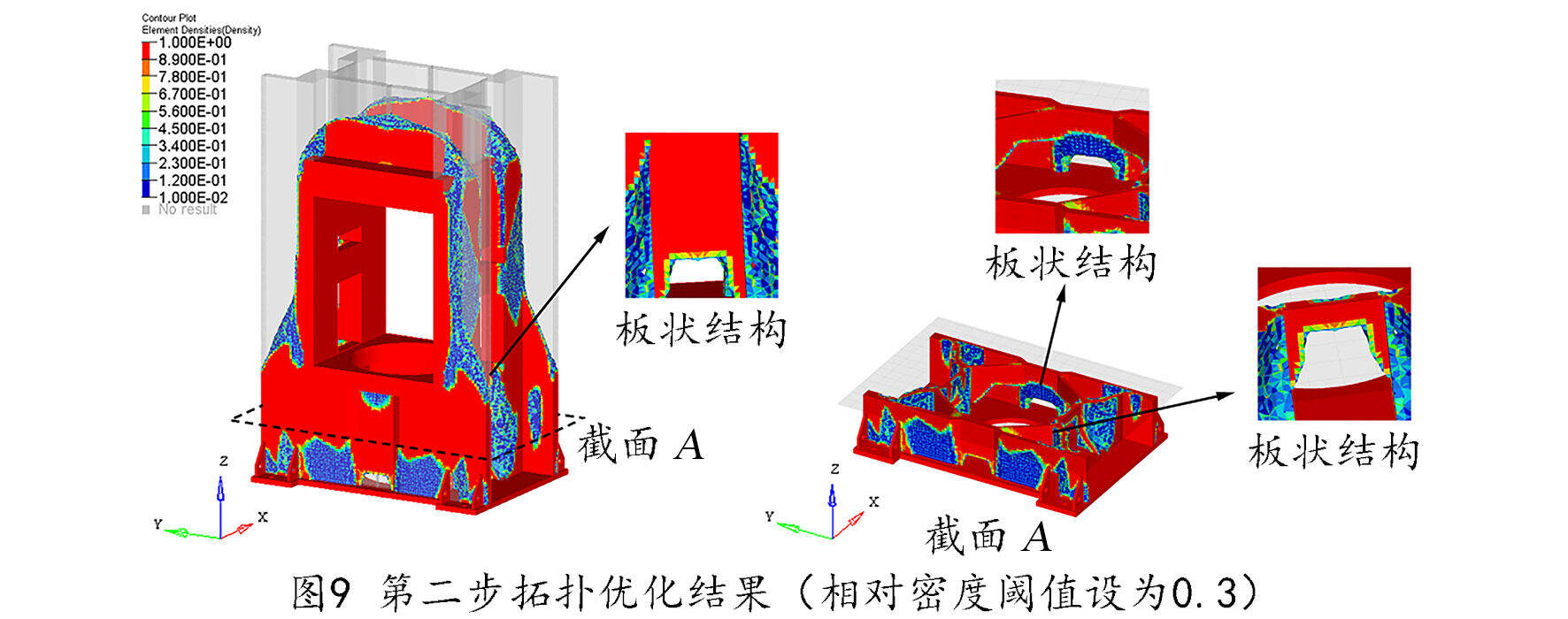
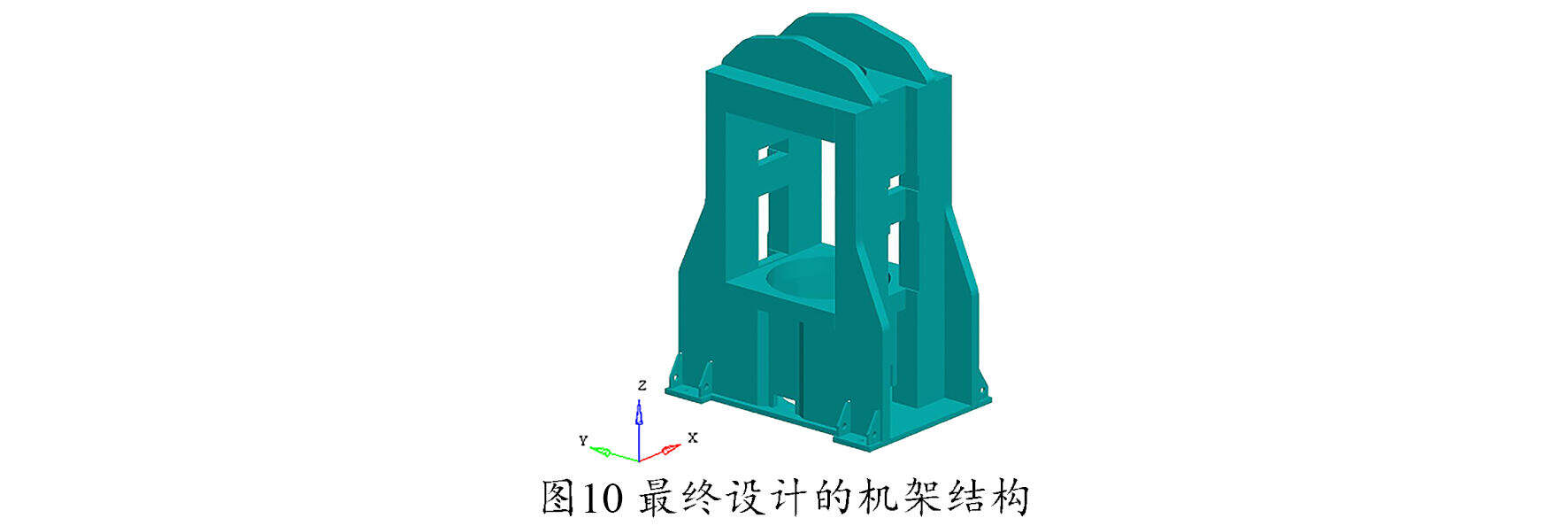
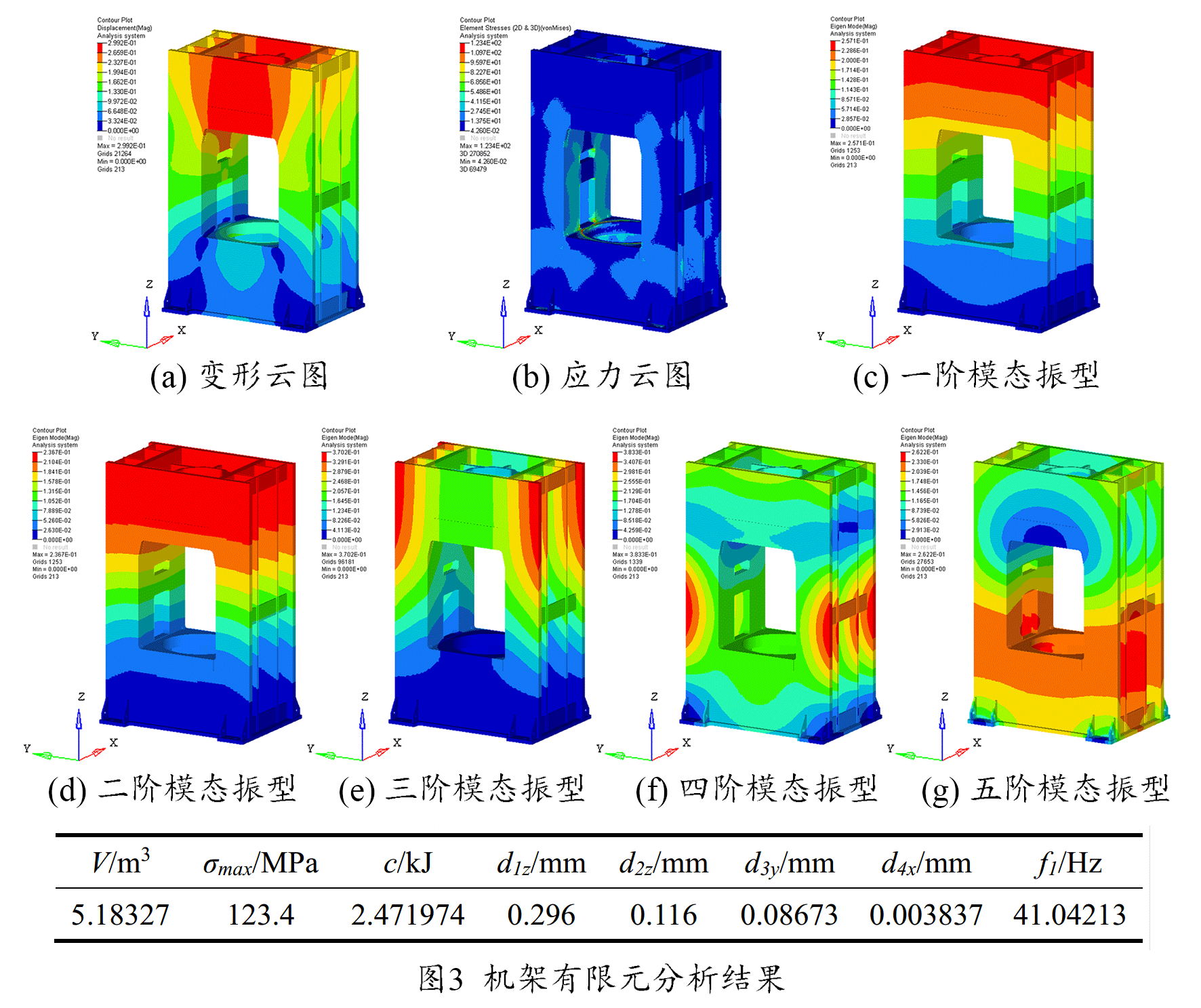
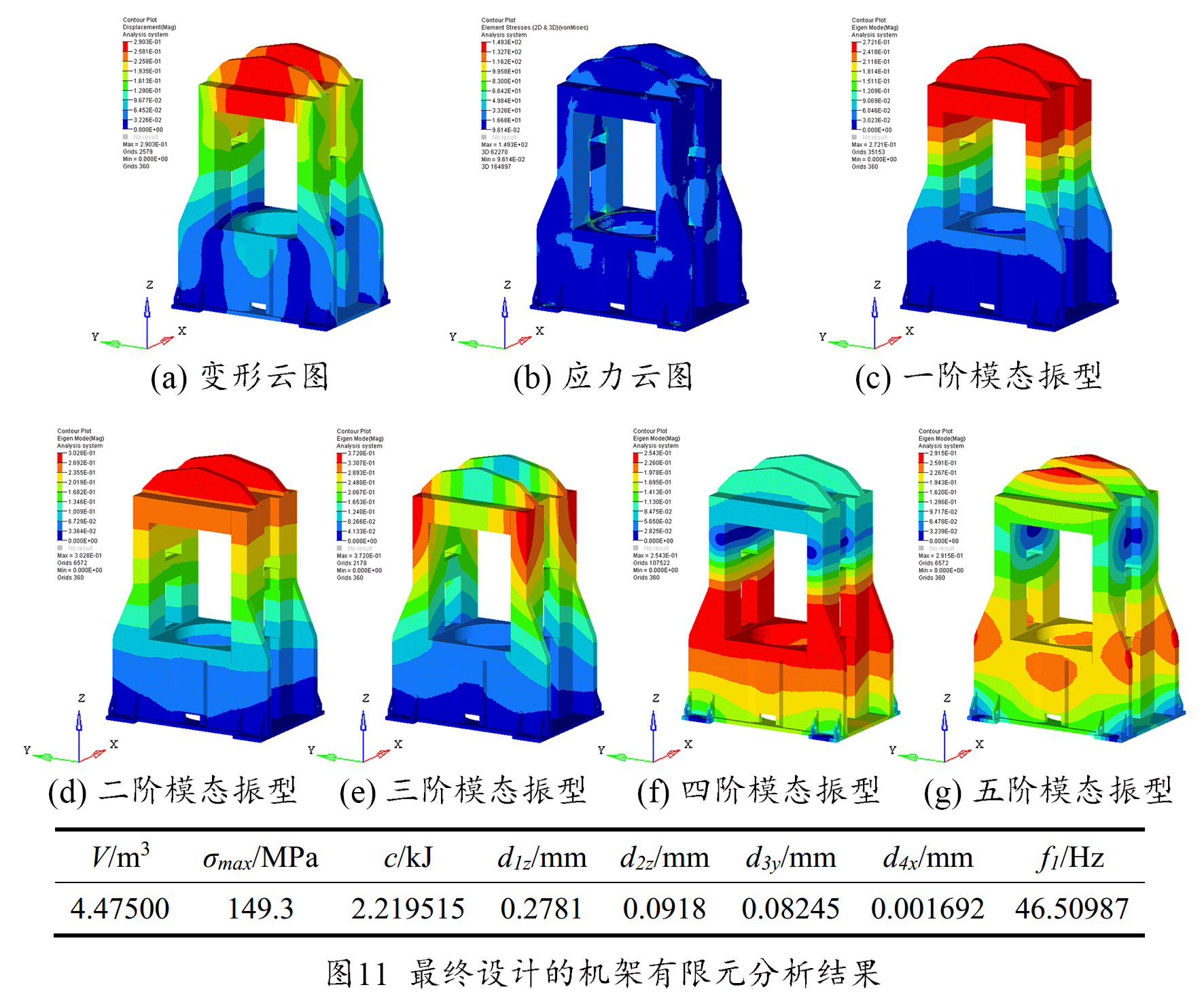
总结:
1)基于所提出的两步拓扑优化方法对12000 kN精冲压力机机架进行了结构优化设计,得到了新的机架结构形式,且优化后的机架结构与原始机架结构相比,在综合性能提高的情况下,体积(或重量)减少了13.66%,成功实现了轻量化;
2)通过分析优化后机架的结构特点,得到两个结论:第一是机架顶部设计为圆弧形,有利于在保证机械性能的前提下,节省材料、降低生产制造成本;第二是材料分布靠近约束部位、重心低,有利于提高结构的动态性能。
我们提供什么服务
汽车、航空航天、装备制造、家电、工程机械等制造业的结构部件优化,轻量化设计。
